产品元器件、零部件的入厂检验,尤其是大批量产品的入厂检验,由于工作量和时间的局限,通常情况下只能采用抽样检验的方式;最常见的方法是选择抽样检验方案,进行随机抽样,然后开始参数测试,再将每一台的测试结果与预期设计性能指标对比,然后根据抽样方案中的合格判据, 确定该批次是通过验收还是拒收。实际上, 这种貌似合理的抽样检验方法里, 即使验收合格,也蕴藏着潜在的隐患问题。
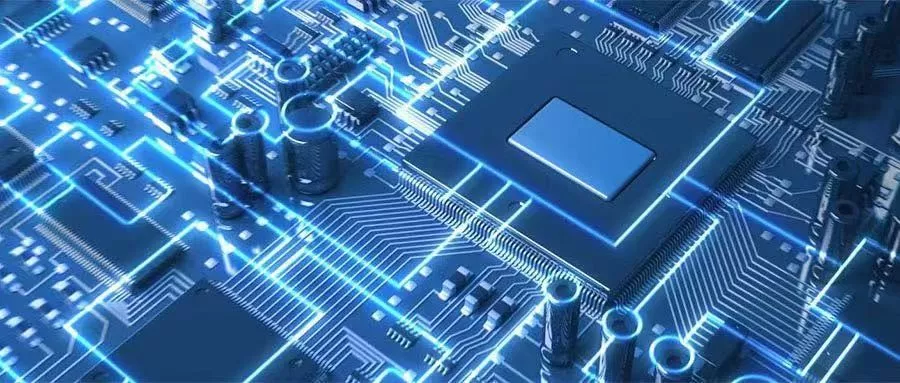
可靠性管理里有一句经典提法“改变=不可靠”,这也是某些产品供货商宁愿在辅助功能上不满足用户,也不愿意升级或者更新已有的成熟产品的原因,因为他们很清楚:
已经定型的设计方案、稳定的加工工艺、不变的生产场地环境、长期熟练使用的成熟生产工具和辅材,一旦发生微小的改变,都有可能引入潜在的隐患因素,而这些因素就有可能在特定的现场应用环境下导致失效。
如果供货商因为种种原因,出现了如器件型号、批次、生产场地变更或者加工工艺改变、出厂异常筛选等因素,而整机厂商却没有发现,则容易因为这些改变而产生潜在隐患,导致某些应用环节故障率的异常增高。
比如某条地铁选用某厂家的成熟产品(计轴产品),首批所供产品开通运营后一直很稳定,第二批在开通一个月内就频繁的出现同一种故障,最后发现是由于第二批板卡中某一个器件更换了供货商导致。因为任何不同厂家生产的相同型号功能的器件,都会存在微小的差异,比如Cin、Ri、Ro、P、上拉电阻……
也正是因为如上的原因,对零部件、器件的质量控制就成为了一个至关重要的课题。采用什么样的检测方法,能较好地发现供应商处可能发生的诸多不稳定问题呢?单靠逐个检验耗时耗力,甚至可能会出现逐个检验都没发现问题,实际却有隐患存在的现象。而解决此问题的有效方法之一即是统计学。
正常生产条件下生产出来的质量稳定产品,对其任一参数的测量结果均应符合正态分布,其原因是每个零部件的生产之间都是相互独立的,检测也是独立的,这种特征的状态参数便符合正态分布。在正态分布里(如图1,本文后续所有示例均以允许误差±5%为例),μ是正态分布的位置参数,描述正态分布的集中趋势位置。而σ描述离散程度,是正态分布的形状参数,σ越大,数据分布越分散,曲线越扁平;σ越小,数据分布越集中,曲线越瘦高。μ±1σ范围内的分布概率是68.3%,μ±2σ范围内的分布概率是95.4%,μ±3σ范围内的分布概率是99.73%。
根据“小概率事件”和“假设检验”的思想,“小概率事件”通常指发生概率< 5%的事件,认为在一次试验中该事件是几乎不可能发生的。由此可见随机变量X落在(μ-3σ,μ+3σ)以外的概率< 5%,在实际中常认为相应的事件是不会发生的,所以基本上可以把区间(μ-3σ,μ+3σ)看作是随机变量X实际可能的取值区间,这称之为正态分布的“3σ”原则。也就是说,正常产品的实际测量结果,必须落在设计所允许的范围(μ-3σ,μ+3σ)之内。
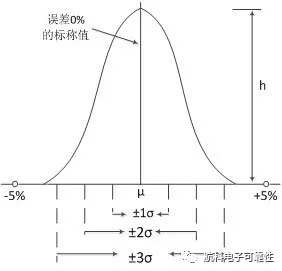
因此,应结合抽样检验方案,选取合适的样本数量,根据实际的检测数据,开展统计分析。下面结合一些数据图形,分析可能出现偏差的原因。
1、一致性变差的正态分布趋势图
如果(图1)是设计或质控所需要的标准正态分布图形式,在实际工作中,会有一种如(图2)的分布图形式,中心点虽没漂移,但数据分布明显发散了。
数据出现这种情况,主要是随机误差影响导致,一般来自于布线、布局,例如施工过程中传感器的电缆布置不符合施工工艺、信号电缆和电源电缆同沟放置、电源的开关频率干扰串扰进入信号线,就容易产生各种随机误差,导致类似这样的测量结果;或者放大电路的模拟信号接地与功率电路或控制数字电路采用了单点串联接地,也会发生类似现象。只要把引入随机干扰的这些原因排除,测量数据分布图就会收缩变成(图1)的形状。
如果供应商来料的测试数据出现类似这样的分布变化,就有可能是供应商偷换货。有的供应商在自己生产能力不足时,会采购或外协其他公司的物料来顶替,然而任何两家的产品批次分布规律是很难完全重合一致的。“改变=不可靠”,任何的改变都可能带来其它不可预知的负面因素,供应商的改变也属于此列,因此对此类物料应该拒收。如果确认该物料确实仍是原厂生产,那么就是这家原厂的质控生产管理出现了巨大问题,应予责令整改方可继续供货。
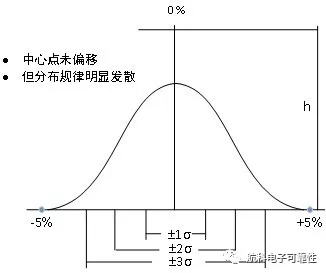
2、一致性增强的正态分布趋势图
(图3)的分布图形式,中心点没有漂移,而且数据分布明显一致性变好了。如果这是单一一台设备在设计过程中测试出来的数据分布情况,就说明设计的效果超出了预期,直接过关即可。
如果是供应商来料中出现类似变化的分布图,则要小心,不要因为质量变好就放行,要找出导致本批次突然变好的原因。因为如果厂家的生产过程没有发生大的工艺变化,不会出现突然明显变好的情况。
如果是供应商偷换原材料,用了采购或外协其他公司的物料来顶替,此批物料建议拒收,因为任何的改变都可能带来其它不可预知的负面因素,即使它在某些指标上变好,也不能掩盖其可能引入其他未知风险的可能。如果确认该物料确实仍是原厂生产,则需搞清其质量提升的缘由,确保不引入可能导致隐患的改变的前提下,可以接收,但仍需对此物料在本厂生产制造以及产品交付后的RAMS报告,质量持续稳定后方能认可其改变。比如前面提到的某条地铁出现的问题,更换板卡元器件后问题得以解决。
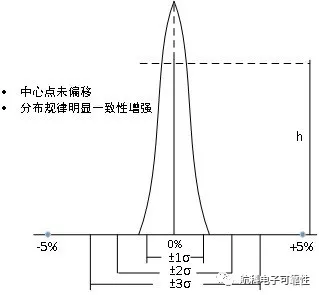
3、中心值偏移的正态分布趋势图
(图4)曲线的一致性程度与(图1)曲线类同,不同的是中心点明显漂移。如果是设计测试数据分析中出现这样的变化,则此问题属于稳态误差,来自于原理设计。在原理图中,通过工程计算,查找到影响此中心值偏移的器件参数,修正后即可将曲线平移成(图1)的形状,至此方可成为理想设计。
如果生产物料的数据统计分析中出现这样的变化,表明该生产企业的质控水平没有问题,很可能是加工设备/工装、测试检验设备/工装,抑或某批次器件供货参数有误造成,不是生产体系问题,只要找到设备或原材料问题的根源,该问题就可迎刃而解。

4、截取后的正态分布图
任何厂家生产的物料、任何设备测量参数的统计分布结果,都应该是服从正态分布的趋势图。如果供货时,收到的物料参数测量统计中,出现如(图5 A)的趋势图,都是不正常的。正常的生产线下来的物料,分布图形式应该如(图5 B),(图5 B)中参数分布在两侧虚线内的物料去了哪里?通常情况下这可能是因为厂家在出厂之前做了测试筛选剔除了。这种情况的物料可以收货,但需跟客户明确,后续正式供货应长期照此办理,并在每次做入场检测和数据统计分析时以该统计图为标准进行监督。
设计中过程的测试数据一般不会出现此种问题,如果有,也不是什么问题,一般是软件进行了筛选限定。仅仅是设计方法的问题,对结果没有妨碍。
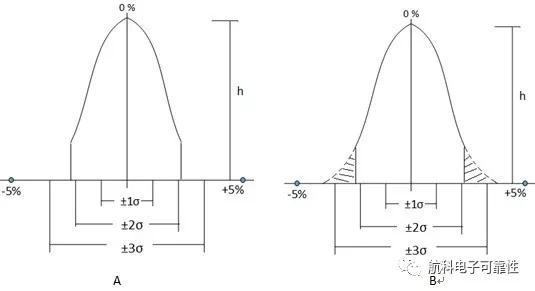
5、双正态分布趋势的叠加图
任何稳定生产厂家的产品都应该是单一正态分布曲线,而(图6)趋势图曲线说明该批次物料为两家生产、或为两条生产线生产、或影响该被测参数指标的零部件为两家供应商供货,且该两家供应商的货品不一致造成的。
这种情况也有可能是物料在库房放置时间较久,参数发生了漂移,最后供货的时候,供货商将新旧物料混在了一起。如果参数没有超标,此类物料可以让步接收,但要是参数超标了,则不可接受,应予退货处理。
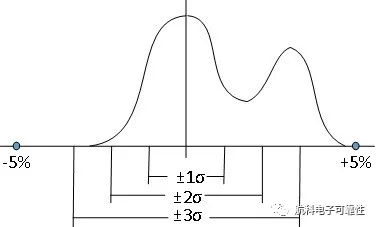
以上分析了同一种曲线在单台产品样机的测试数据分析、或批量供货物料的数据统计分析中的成因和应用价值。在实际工作中进行时,无论是单台研发样机的测试验收,还是批次产品质控过程的一致性验收,即使在具体参数上与标准要求对比没有问题,但通过这种数据统计分析方法,仍可以从中发现隐患点,并能指导提出具体的改进措施。
如下给出某信号设备仪表中用到的稳压二极管的分析方法。
某信号仪表中,用到了一款原产于美国的稳压二极管,质量稳定性一直很好。后来因为成本方面的考虑,做了物料国产化替换,替换后就出现了批次性质量问题,有约0.6%左右的击穿故障概率。经过对两个厂家的物料取样各50只,进行参数测试逐一对比,均未发现有超出数据手册的指标。经过了各种可靠性测试实验项目,也未发现器件质量问题。最后做了统计学分析实验,分布图如下:
统计实验做了两个参数,一是通过调节稳压管上的VZ电压,使每只管子上的漏电流保持一个相同的值0.5mA,然后记录下各管子在同一漏电流下的VZ值,统计分布图分别如(图7A国产高失效稳压二极管VZ参数分布图)和(图7B 美国产低失效稳压二极管VZ参数分布图)
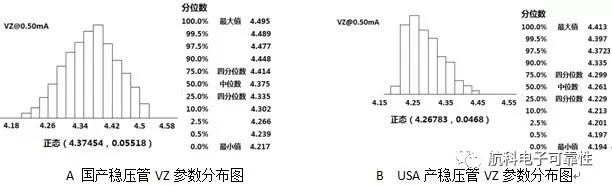
由(图7)中分析可以看出,美国产器件的正态分布趋势不完整,左侧有部分边缘参数值分布空白,这是典型的筛选剔除特征,说明器件厂商出厂前做了筛选实验,剔除了部分其认为会比较容易失效的器件。
为做进一步验证确认此分析结果,又对以上两厂家的样本做了VZ=3V时的漏电流参数分布测试分析如(图8)所示。(图8A)中的分布为近似正态分布,而美国产器件的漏电流分布图(图8B),中右侧有部分边缘参数值分布空白,这仍是典型的筛选剔除特征,再次确认了器件厂商出厂前做了筛选实验,剔除了部分其认为会比较容易失效的器件。
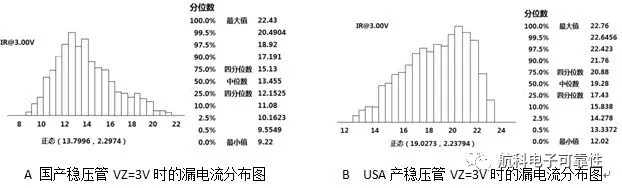
由以上分析,则可找到使国产替换器件质量提升的的一个研究方向,即要求厂家在出厂前,也做类似的器件参数分布筛选,将Ileak固定值时的VZ边缘值器件、VZ固定值时的Ileak边缘值参数器件做筛选剔除,并适用几个批次,同时保持紧密跟踪成品后的质量反馈数据,如果0.6%的指标明显下降,则证明此方法有效可行。
以上描述了运用统计分布规律帮助发现设备中器件或模块、整机质量问题隐患的方法,既适用于研发样机的质量分析,也可用于生产过程的质量控制。
数理统计与概率论这门学科,与工程实践结合,可以很好地帮助我们发现不少问题,提供很好的技术决策思路和管理手段。由此也佐证了一句话:"数学是最美丽的语言,他与工程实践的结合将会带来质的提升",非常值得持续挖掘下去。
本文转载自:航科电子可靠性
本文刊于《电子产品世界》2018.11期。作者为赵慧娟、武晔卿。但限于微信发文限制只能显示一位作者。特此声明。
免责声明:本文为转载文章,转载此文目的在于传递更多信息,版权归原作者所有。本文所用视频、图片、文字如涉及作品版权问题,请联系小编进行处理。